TECH BASICS: LESSON 7
7) How small is small?
Read the video transcript below the video, or download all video transcripts in this course here.
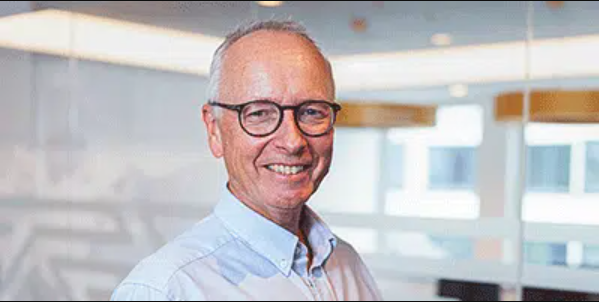
Link to soldering video: SMT Pick-and-Place Process
Conductors: Materials that allows electrons to pass through. In PCBs, conductors connect components.
Insulation: Materials that do not allow electrons to pass through.
Vias: Vertical holes in a PCB. They let electrons move between layers.
Resistance: A measurement of how hard it is (or not) for electrons to move in
a conductor.
To plate: To apply a thin layer of metal.
Pads: Places on the PCB’s surface to solder components.
Soldering: Melted metal to connect a component to the pad.
Prepreg: Fiberglass pre-impregnated with epoxy. It is both glue and insulation between layers of copper conductors.
Laminate: Layers of cured prepreg.
Core: Laminate with copper foil on both sides, used inside the PCB.
Transcript
7) How Small is Small?
How small is small? NCAB’s customers want PCBs that are small and perfect. But how small are we talking about?
This is an ordinary toothpick. And this is a 2-layer, standard 1.6 mm, PCB from the side. Can you see it?
I’ll expand them, so they are easier to see. The toothpick is 2 mm thick, but with PCBs, millimeters are too big to be practical. For measures below 1 mm, we use microns instead which are 1,000 times smaller.
Here is the laminate, 1.5 mm, and the copper, 35 microns on each side. If there were inside layers in this PCB, that copper would be even thinner, down to 18 microns. And then the soldermask, 10 microns each side. So, a standard 2-layer PCB thinner than a toothpick, is 1.6 mm, but we often make them even thinner.
DENSITY How many components can fit onto this area |
Everything around PCB is small. The red and yellow capacitors and resistors in the TV from the 50s, have now become so small that they can barely be seen without a magnifying glass.
A key design measure for customers is the density of the PCB. And more components mean more function on less space.
Just look at this PCB (with components mounted) inside an iPhone; it gives you an idea of density. Each of these small components has two areas that connect pads to PCB. This PCB can only be made in very few factories globally.
Just imagine fastening the smallest components in thousands to one single PCB! That’s the customer’s job,
PANELS Sheets of identical PCBs that make the customer’s handling more efficient. |
and our job is to make the customer’s job easy as possible. So, how can we make tiny PCBs easier to handle? Well, instead of delivering PCBs in one-by-one, we can make panels. A panel can be moved around as one piece so that customers don’t have to handle one PCB at a time. This helps them with efficiency and cost of assembly.
Components are placed by robots, and this process is amazing! I strongly recommend that you watch a video (there is a link after this lesson) with a robot at work. One such robot can place 33,000 components in an hour!
So, who can supply these little miracles? Well, NCAB can, and one reason why we do it so well is how we cooperate with our factories.
Even though we don’t own any factories at NCAB, we are deeply involved in the details of manufacturing. Our Factory Management people know exactly which factories are the best at which technologies, and are often personally on site to advise factories on how to achieve the best quality. We see everything, and that’s what the red eye in our logo stands for.